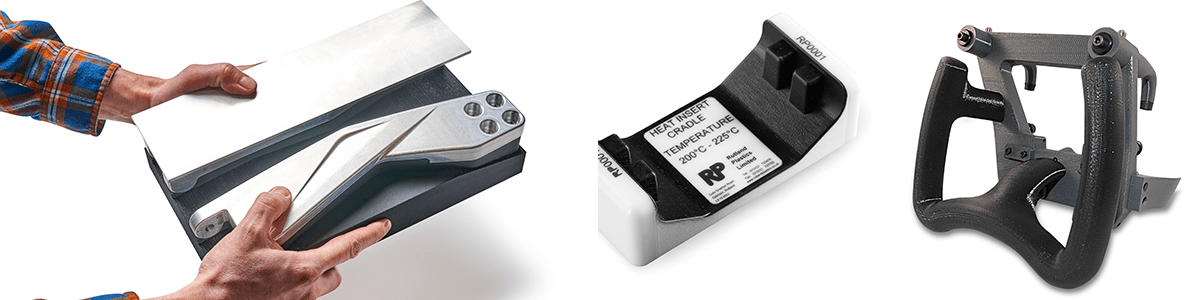
3D nyomtatott befogó készülékek és ülékek gyorsabb gyártása
A modern gyártás területén a pontosság és a hatékonyság a legfontosabb. A precíz és konzisztens eredmények elérése az összeszerelési, megmunkálási, hegesztési és ellenőrzési folyamatokban nagymértékben függ a rögzítés hatékonyságától. A befogó készülékek, a szerelési segédeszközöktől kezdve az ellenőrző szerszámokig, kulcsfontosságú szerepet játszanak a stabilitás, az igazítás és a minőség biztosításában a gyártás során. Az egyik innovatív megközelítés, amely forradalmasítja a rögzítési módszereket, a 3D nyomtatási technológia integrálása a befogó készülékek és ülékek gyártásába.
A befogó készülékek funkciója
A befogó készülék a munkadarabok stabilizálására szolgáló mechanizmusokkal vagy támasztékokkal kialakított alapkeret. Jelentősége a különböző gyártási folyamatok során a helyes eredmények biztosításában rejlik, ezáltal fokozva a termelékenységet, a biztonságot és a termékminőséget.
A 3D nyomtatás szerepe a befogó készülékek fejlődésében
A 3D nyomtatási technológia integrálása a befogó készülékek és ülékek gyártásába paradigmaváltást jelent. Ez az innovatív megközelítés páratlan előnyöket kínál, lehetővé téve az igényekre szabott, egyedi befogó készülékek gyors és költséghatékony gyártását. A 3D nyomtatás rugalmassága révén elérhető a bonyolult geometriák tervezése és a munkadarabok különböző specifikációihoz való alkalmazkodás.
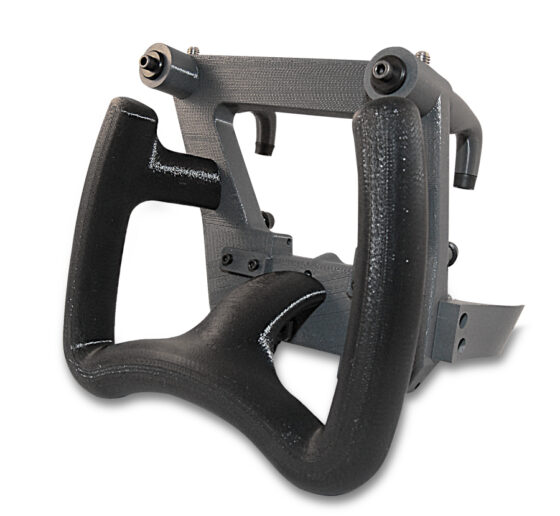
A 3D nyomtatott befogó készülékek előnyei
A 3D nyomtatás alkalmazása a befogó készülékek gyártásában jelentősen csökkenti az átfutási időt, a gyártási költségeket és az anyagpazarlást. Ezenkívül egyszerűsíti a könnyű, mégis robusztus, összetett geometriájú befogó készülékek készítését, amelyeket hagyományos gyártási módszerekkel nehezen, vagy egyáltalán nem lehet megvalósítani. A testreszabási lehetőségek gyakorlatilag korlátlanok, így a befogó készülék gyorsan hozzáigazíthatók a változó gyártási követelményekhez.
A befogó készülékek típusai
A gyártók különböző típusú befogó készülékeket készítenek, amelyek mindegyike speciális alkalmazásokhoz igazodik.
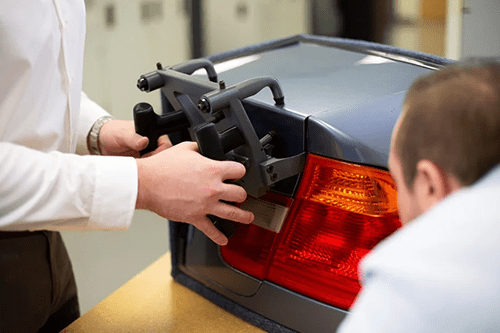
Szerelő ülékek:
A szerelési műveletek során az ülékek nélkülözhetetlen segédeszközök, megkönnyítik az alkatrészek pontos igazítását és pozicionálását. A 3D nyomtatott befogókészülékek és ülékek alkalmazása az összeszerelési feladatokban nagyobb sebességet, pontosságot és kevesebb hibát eredményez, ami különösen az olyan iparágakban előnyös, mint az autóipar, az elektronikai szektor és a repülőgépipar.
Ellenőrző ülékek:
A minőségellenőrzés szempontjából kritikus fontosságú ellenőrző ülékeket olyan berendezésekkel együtt használják, mint a koordináta-mérőgépek (CMM), hogy a munkadarabokat pontos mérés és elemzés céljából rögzítsék. A 3D nyomtatás alkalmazása az ellenőrző ülékek gyártásába növeli a pontosságot, a megismételhetőséget és a hatékonyságot, ami előnyös többek közt a repülőgépipar, az elektronikai szektor és az autóipar számára.
Jelölő ülékek:
A gyártási folyamatok megkövetelik a munkadarabok pontos és következetes jelölését. A jelölő ülékek, beleértve a lézeres jelölésre optimalizáltakat is, biztosítják a kiváló minőséget, megismételhető jelöléseket, például márkajelzéseket, sorozatszámokat vagy vonalkódokat. A 3D nyomtatott jelölő ülékek alkalmazása növeli a hatékonyságot és a következetességet az olyan iparágakban, mint a repülőgépipar, elektronikai szektor és az autógyártás.
Hegesztési ülékek:
A hegesztési folyamatok során az ülékek döntő szerepet játszanak a munkadarabok stabilizálásában és igazításában, biztosítva a pontos hegesztési varratokat. A 3D nyomtatott hegesztési ülékek használata javítja a hegesztés minőségét, a megismételhetőséget és a termelékenységet, kiszolgálva az autóipar, a repülőgépipar, az építőipar és a fémfeldolgozó ipar igényeit.
Összegzés
A 3D nyomtatás és a befogó készülékek közötti szinergia átalakítja a gyártási folyamatokat, páratlan pontosságot, hatékonyságot és költséghatékonyságot kínálva. Ahogy az iparágak egyre inkább elfogadják ezt az innovatív megközelítést, az összeszerelési, ellenőrzési, jelölési és hegesztési folyamatok termelékenységének és minőségbiztosításának lehetőségei tagadhatatlanul javulnak.
A 3D nyomtatással készült befogó készülékek és ülékek integrálása a gyártási minőség új korszakát jelenti, forradalmasítva azt, ahogyan az iparágak biztosítják a pontosságot és a következetességet a gyártási eljárásaikban.
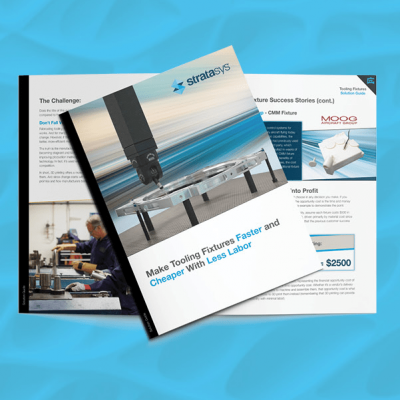
Töltse le a 12 oldalas, magyar nyelvű Megoldási útmutatót!
Ismerje meg, hogyan hozhat az additív gyártás új lendületet a befogó készülékek gyártási folyamatába, miközben növeli az idő- és költségmegtakarítást!