Idén is ipari 3D szkenner és 3D nyomtató újdonságokkal várjuk a VARINEX standon 2024. május 7-10. között Magyarország legnagyobb üzleti ipari találkozóján, a Ipar Napjai, Mach-Tech és Automotive Hungary 2024 kiállításon.
Időpont: 2024. május 7-10 (keddtől péntekig)
Nyitvatartás: keddtől csütörtökig: 10:00-17:00, pénteken 10:00-16:00
Regisztráljon csütörtöki előadásunkra, hogy megtudja, hogyan gyárthatók 3D nyomtatással a kritikus fontosságú alkatrészek!
Magyarországon először az Ipar Napjain mutatjuk be élőben az akár 1171 mm hosszú alkatrészek 3D nyomtatására is képes Stratasys F770 3D nyomtatót ABS és ASA alapanyagokkal!
Megismerheti a kompozitgyártásra optimalizált Stratasys F370CR gyártóberendezést, Nylon CF-10 szénszálas alapanyaggal, amely 67%-kal erősebb, és 190%-kal merevebb az alappolimernél!
Találkozhat a fröccsöntéshez hasonló kiváló felületi minőséggel dolgozó Origin One 3D nyomtatóval, amely valódi DLP technológiát használ.
Ismerje meg a legújabb alapanyagokat, amelyek egyre szélesebb alkalmazási területet nyitnak meg, és vegye kézbe a 3D nyomtatott alkatrészeket standunkon. A kiállítás alatt 3D szkenner bemutatóval is várjuk.
Nézze meg működés közben a gyors és hatékony 3D szkennereket és 3D nyomtatókat, tegye fel szakmai kérdéseit szakértő kollégáinknak!
A Pavilon 306B stand
Ideje NAGYBAN gondolkodni!
Stratasys F770 3D nyomtató magyarországi premier
Magyarországon először az Ipar Napjai Kiállításon mutatjuk be élőben az akár 1171 mm hosszú alkatrészek 3D nyomtatására is képes Stratasys F770 3D nyomtatót!
Nézze meg működés közben ezt a gyors és hatékony additív gyártóberendezést a VARINEX standon!
Az előadást se hagyja ki!
Hogyan oldható meg a kritikus fontosságú alkatrészek gyártása 3D nyomtatással?
Ha kíváncsi a válaszra, feltétlenül jöjjön el Fehér Zoltán, a VARINEX műszaki igazgatójának előadására!
2024. május 9. csütörtök, 11:00-12:00
A Pavilon AI 115. terem
A részvétel ingyenes, de regisztrációhoz kötött! A helyek száma korlátozott, regisztráljon most!
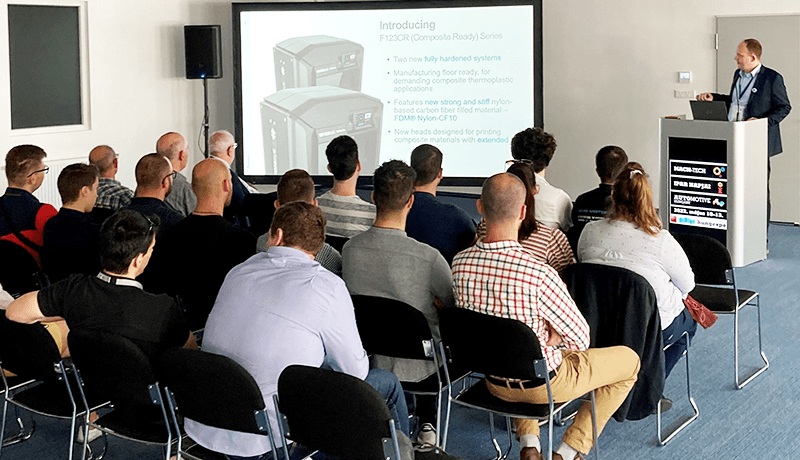
Az előadás után süteménnyel és kávéval várjuk további beszélgetésre és kiállításunk megtekintésére az A pavilon 306B standon!
Mivel várjuk a VARINEX standon?
- Gyors és megbízható 3D nyomtatók működés közben
- 3D szkenner bemutató
- Előadás a kritikus fontosságú alkatrészek gyártásáról 3D nyomtatással
- A legújabb 3D nyomtató alapanyagok
- Kötetlen beszélgetés, 3D technológiai szaktanácsadás
- 3D nyomtatott alkatrészek 6 ipari technológiából